Hoe verloopt het testen van een elementengevel op lucht-, wind-, en waterdichtheid?
Interview | Rob Grein, Projectmanager Reynaers Aluminium
Hoe waarborg je wooncomfort? Wooncomfort, laten we het omschrijven als een gevoel van behaaglijkheid. Er zijn verschillende factoren die dat kunnen beïnvloeden. Zo wil je als bewoner geen tocht, geen lekkende kozijnen of geen hoge luchtvochtigheid in je woning. Daarom is het testen van bouwsystemen – in dit geval aluminium systemen voor ramen, deuren en gevels - zo belangrijk. Die geven een kwaliteitsverklaring die de prestaties in de toepassing beschrijft van een (maatwerk) systeemoplossing. Op de Reynaers Campus in Duffel spreken we met Rob Grein, Projectmanager bij Reynaers Aluminium. Hij neemt ons mee in het testproces van aluminium systemen, van standaard tot projectspecifieke testen.
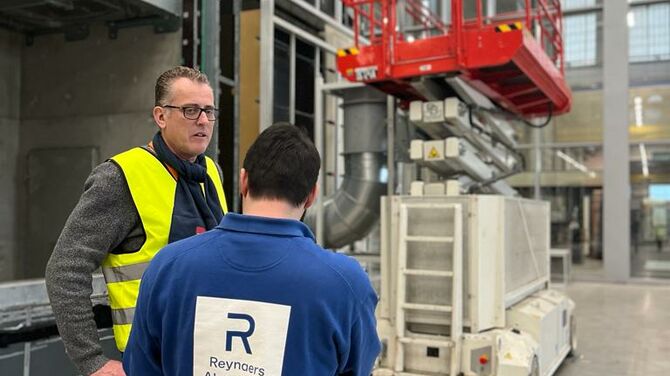
Rob Grein bij aanvang van de test op de Reynaers Campus in Duffel.
‘Wij testen altijd onze systemen’, opent Rob het interview kort maar krachtig. ‘Die systemen toetsen we op bepaalde klassen die volgens de Europese norm (EN, red.) gelden. Het is van cruciaal belang om ervoor te zorgen dat systemen veilig, van hoge kwaliteit en betrouwbaar zijn. Het comfort voor bewoners speelt daarin een belangrijke rol. Op deze manier zorgen we er samen met onze partners voor dat we bouwen aan een comfortabele, veilige en duurzame leefomgeving’.
Van standaard tot projectspecifiek
Zo is ook de nieuwe elementengevel ElementFaçade 7 (EF7) getest. Deze toekomstbestendige elementengevel combineert flexibiliteit, ontwerpvrijheid en betrouwbare prestaties in één oplossing. Een onafhankelijke keuringsinstantie, bijvoorbeeld SKG-IKOB of UL, sluit aan bij de officiële test. Komt daarvoor groen licht, dan kan een systeem op de markt gebracht worden. ‘Deze basis elementengevel is ook getest voor de UK (CWCT, red.) en USA (ASTM, red.) normen waardoor het basissysteem in Europa, de UK en de USA mag worden toegepast’, voegt Rob toe.
ElementFaçade 7 is uitstekend geschikt voor hoogbouwprojecten en voldoet aan de strengste normen rondom isolatie en duurzaamheid. ‘Met alle betrokken partijen richten wij ons in het ontwikkelproces op zo toekomstbestendig mogelijk bouwen. Klimaatveranderingen zetten door, waardoor we te maken krijgen met bijvoorbeeld overstromingen of stormen. De veiligheid en het wooncomfort voor de toekomstige bewoners nemen daardoor in de ontwikkeling een belangrijke plaats in’, vertelt Rob.
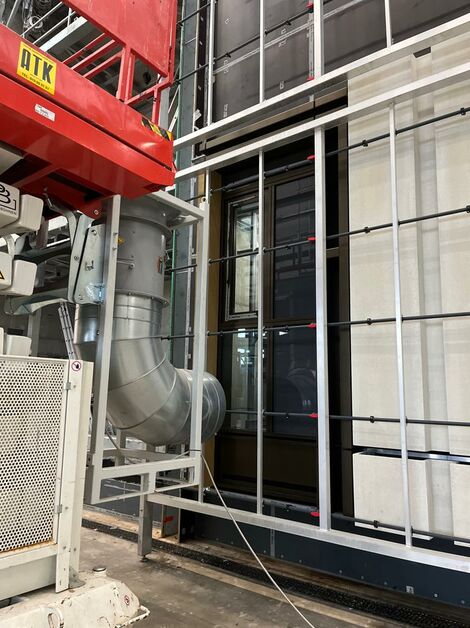
Niet alleen Reynaers Nederland, maar ook alle andere Reynaers vestigingen vanuit de hele wereld maken gebruik van deze unieke testlocatie in Duffel. Het testcentrum is het grootste particuliere testcentrum van Europa.
Testen van een projectspecifieke elementengevel
Gaat het om speciaal element dat Reynaers Aluminium samen met partners uit de bouwkolom heeft ontwikkeld, dan vinden er specifieke projecttesten plaats. ‘Dit was ook het geval bij een unieke projectoplossing voor een groot project in de UK. Hierin hebben wij de CWCT (Centre for Window & Cladding Technology, red.) normen voor testen gehanteerd. Het gaat om een maatwerkoplossing waarin als basis de elementengevel EF7 is verwerkt’, zegt Rob.
Vandaag zijn we in Duffel getuige van dit bijzondere proces. ‘In eerste instantie wordt de projectspecifieke elementengevel op ware grootte in een hoge testopstelling geplaatst. Dit om de prestaties van de gevel in de praktijk te bepalen. Het is noodzakelijk om eventuele gebreken of onvolkomenheden in de bouwconstructie vroegtijdig te identificeren en te corrigeren’, licht Rob toe. ‘Zo voorkomen we bouwfouten’.
Procedure met vastgestelde normen
De toetsing van het systeem op de vooraf gestelde normen neemt meerdere dagen in beslag. Het hele proces verloopt onder toeziend oog van een geaccrediteerde partner. Aan de hand van een specifieke procedure met standaarden, opgesteld door in dit geval The CWCT, wordt de elementgevel aan verschillende testen onderworpen. ‘In deze procedure wordt ook de testvolgorde per onderdeel bepaald’, gaat Rob verder. ‘Wist je dat de verschillende fasen en de volgorde daarin zelfs verschillen per land of project? De uitdagingen die je kunt tegenkomen tijdens en na het proces zijn dus geheel afhankelijk van de gestelde standaarden, de volgorde daarin en uiteraard de resultaten.’
Testdag 1
Luchtdichtheid van het element
Testdag 1 start met het beoordelen van de luchtdichtheid van de gevel, zowel op positieve als negatieve druk. Rob neemt ons stap voor stap mee in het proces en vertelt: ‘Er wordt 600 Pascal lucht, zowel positief als negatief, op het element gezet. Dat is niet in één keer 600 Pascal, maar opbouwend in stappen. Om er zeker van te zijn dat het element een langdurige belasting aan kan, hebben we bepaalde onderdelen in het testproces meerdere malen herhaald. Hoofdzakelijk om vast te stellen of het element na de bepaalde belasting nog steeds de eerste test haalt. De toetsing is erop gericht om de meest heftige weersomstandigheden na te bootsen.’ Dit onderdeel van de test van de projectoplossing in EF7 wordt met een positief resultaat afgesloten.
Statische watertesten
In het tweede onderdeel komen de intensieve statische watertesten aan de orde. ‘Dit doen we om de infiltratie van water uit te sluiten’, vertelt Rob. ‘Het water komt uiteindelijk, onder druk tot maximaal 600 Pascal op de elementengevel. Die 600 Pascal kun je vergelijken met een zeer zware storm. Denk aan windkracht 11, een hoge belasting dus!’ Er wordt voor dit specifieke project op deze hoge belasting getest vanwege de gestelde eisen. Denk hierbij aan de locatie, het gebied, de hoogte van het gebouw en (on)bebouwde omgeving.

Het water komt uit een zogenaamde “rig” met sproeikoppen, ook wel een spraybar genoemd.
Het water komt uit een zogenaamde “rig” met sproeikoppen, ook wel een spraybar genoemd. In het begin wordt de gevel voor vijftien minuten met een bepaalde hoeveelheid water belast, zonder druk. Daarna wordt er vijf minuten statisch ‘ingeregend’ op 50 Pascal, tot uiteindelijk een druk van 600 Pascal. Zo’n stap gaat in fasen van vijf minuten en gecontroleerd tot een totaal van vijfenvijftig minuten is bereikt. ‘Ook dit onderdeel is geslaagd’, vertelt Rob opgelucht. ‘Hierna gaan we naar een bijzonder onderdeel, namelijk de dynamische watertest’.
Testdag 2
Dynamische testen op waterdichtheid
Op dag 2 wordt als eerste bepaald of het element bestand is tegen de meest heftige weersomstandigheden. Rob licht deze stap verder toe: ‘Het dynamische testen, waarin we de beweging van water nabootsen, doe je om zo dicht mogelijk bij de werkelijke weersomstandigheden te kunnen komen. We maken in deze fase daarom gebruik van een dynamische fan. Dat moet je zien als een hele grote ventilator’. Bij dit onderdeel wordt water met hoge druk aangebracht op het element om te bepalen of er waterinfiltratie optreedt. ‘Hier zetten we dus de dynamische fan voor in. En zoals je ziet staat de fan op zeer korte afstand van de testopstelling.’
De test begint met vijftien minuten inregenen, waarbij vervolgens de gevel twee keer vier minuten wordt belast. De dynamische fan beweegt verticaal omhoog en omlaag over twee banen en voert zo een aanzienlijke belasting met wind en water op de gevel uit. Rob vervolgt zijn verhaal: ‘Er wordt tijdens dit onderdeel ook bepaald of het element goed is afgedicht. Hiervoor zetten we de “hose test”, in. Zie dit als een tuinslang die we specifiek op de naden zetten. Dit onderdeel wordt straks op de bouwlocatie nogmaals uitgevoerd.’
Benieuwd naar het verloop van de dynamische watertest?
Bekijk hier rechts de video.
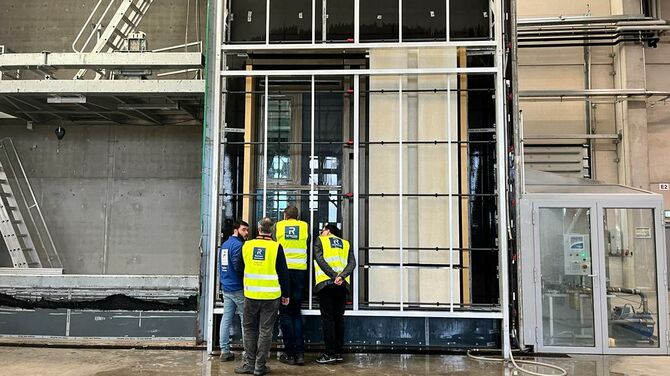
Het team van experts bekijkt het resultaat na de dynamische watertest.
De uitslagen
‘Het zijn testen die je niet elke dag uitvoert en ik ben dan ook heel benieuwd naar de testuitslagen’, benoemt Rob. Het team van experts neemt een kijkje bij de opstelling en constateert na inspectie toch enige waterinfiltratie. Dat betekent dat de test is gefaald. ‘Dit geeft dus het belang van testen aan. Want theoretisch maak je een benadering, in de praktijk moet zo’n oplossing ook worden toegepast’, zegt Rob.
Corrigerende werkzaamheden
De test wordt gestaakt en het team van experts onderzoekt de oorzaak van de gefaalde test en gaat samen om tafel voor een oplossing. ‘In deze fase hebben we met de experts van Reynaers Aluminium gekeken welke aanpassingen nodig zijn. Hieruit voortkomend is ons plan van aanpak voorgelegd en goedgekeurd door de geaccrediteerde partner’. Dankzij jarenlange ervaring en kennis kwam het team tot een gedegen oplossing voor de opdrachtgever. ‘En dit komt uiteindelijk de samenwerking met alle partijen in het proces ten goede’, vult Rob aan.
Na de uitgevoerde herstelwerkzaamheden worden de vooraf genoemde testfasen opnieuw gestart. Zowel de luchtdichtheid-, als de statische en dynamische watertesten laten op dag 1 en 2 een positief resultaat zien. Op dag 3 kan het laatste testonderdeel beginnen: de “impact resistance” fase.
Testdag 3
Impact resistance fase
Deze impactweerstandstest is een methode om de weerstand van materialen tegen impactbelastingen te beoordelen. Er wordt bepaald hoe goed het materiaal bestand is tegen stoten, vallende voorwerpen of andere impactkrachten die in een (bouw)omgeving kunnen voorkomen. Met een speciaal ontworpen valsysteem wordt een “soft en hard body impacttest” uitgevoerd. Hierbij laat men het gewicht letterlijk “vallen” tegen de elementengevel. Ook dit onderdeel wordt met succes afgerond.
Demontage
De laatste fase van het testproces is bereikt. ‘In deze fase gaan we aan de slag met demontage. De keuringsinstantie bepaald hoe de demontage uitgevoerd moet worden. In dit geval zagen we het element doormidden en worden er gaten in het element geboord. Zo kunnen we checken of er bijvoorbeeld water in de profielen zit’, vertelt Rob.
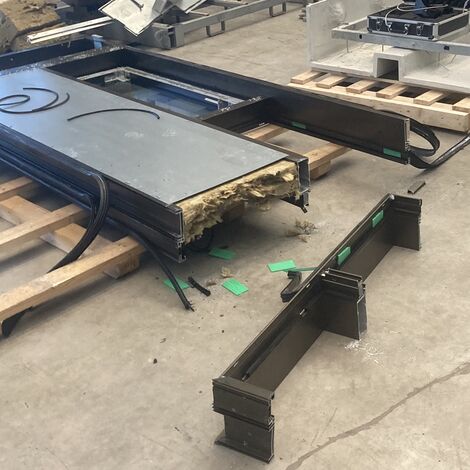
Demontage van het element.
Is de test geslaagd?
Na een aantal spannende testdagen vertelt Rob opgelucht: ‘Alle testonderdelen zijn geslaagd. Het is nu wachten op het officiële testrapport. Binnenkort staat er ook een bezoek aan de bouwlocatie gepland. Het is natuurlijk de kers op de taart om daar dan het geteste element ook in het project te zien.’ De agenda van Rob loopt daarnaast alweer vol met nieuwe aanvragen voor projectspecifieke testen. “Op naar nog meer geslaagde testresultaten”, sluit Rob af.
Hulp nodig bij het realiseren van uw project?
Neem contact op met uw rayonmanager of projectadviseur via telefoonnummer +31 (0)492 - 56 10 20. Zij helpen u graag.
Colofon
Knowhow@Reynaers ontstaat in samenwerking met:
Tekst: Marketing & Communicatie Reynaers Aluminium en StudioLetters